Terminal 3


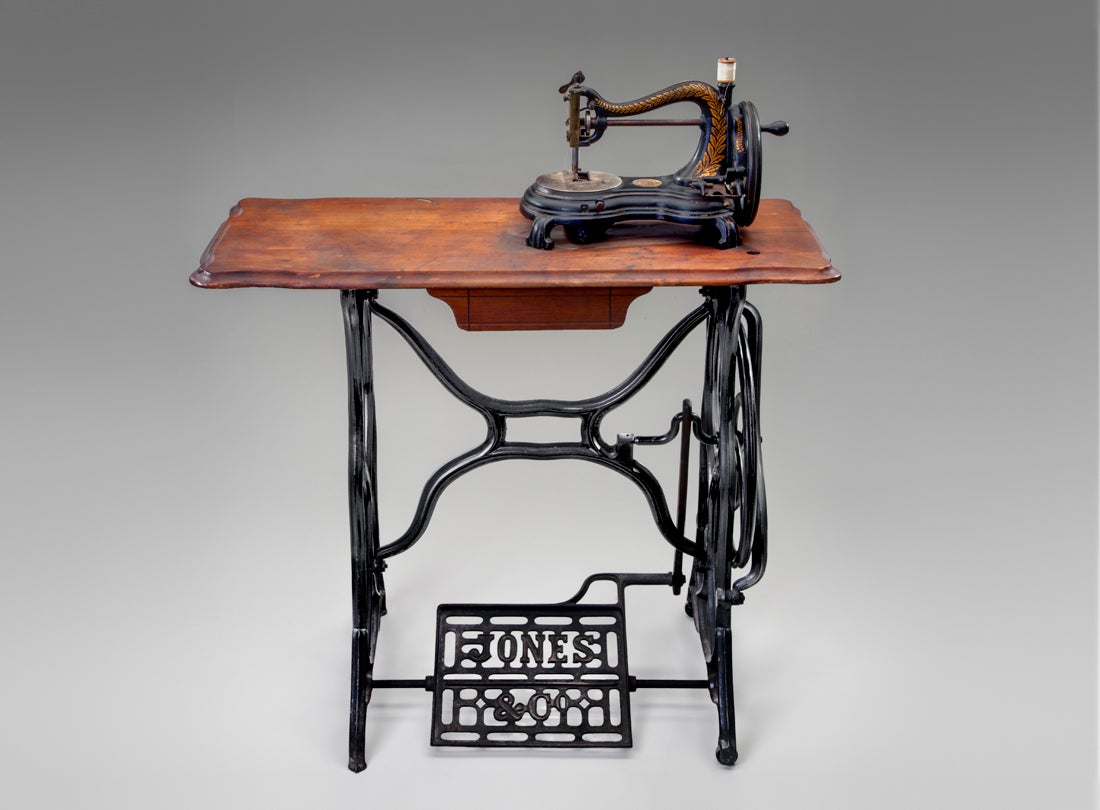



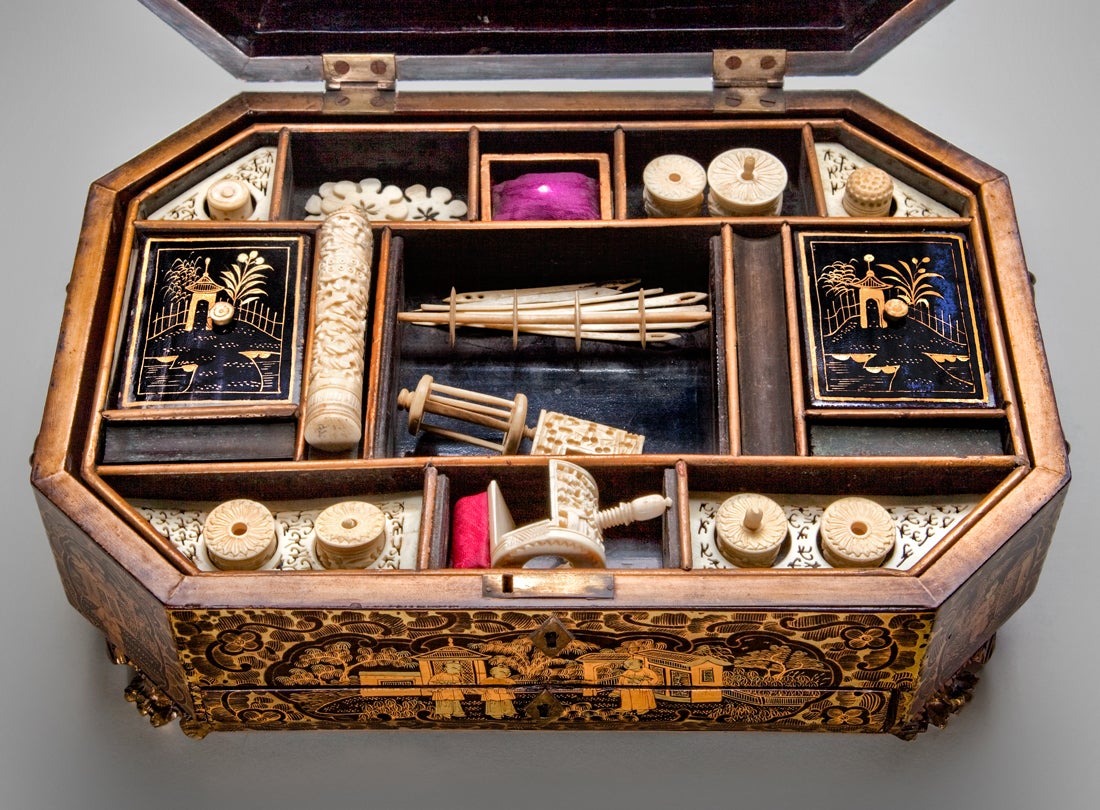




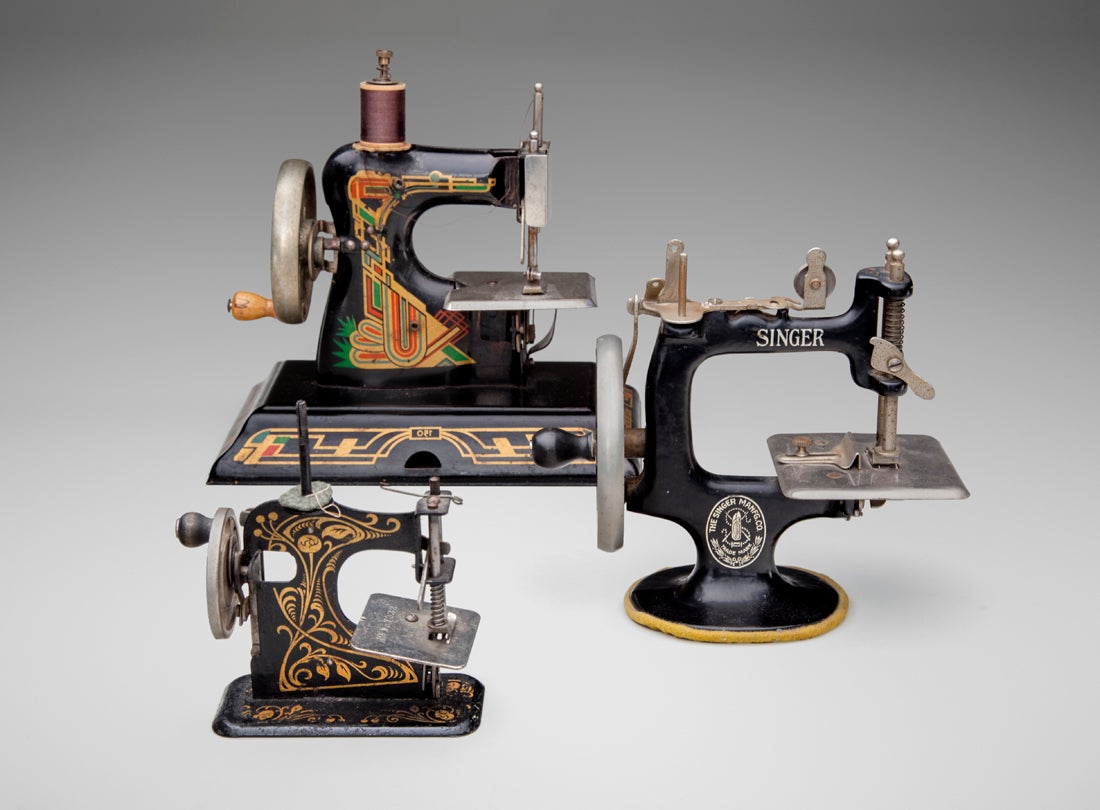





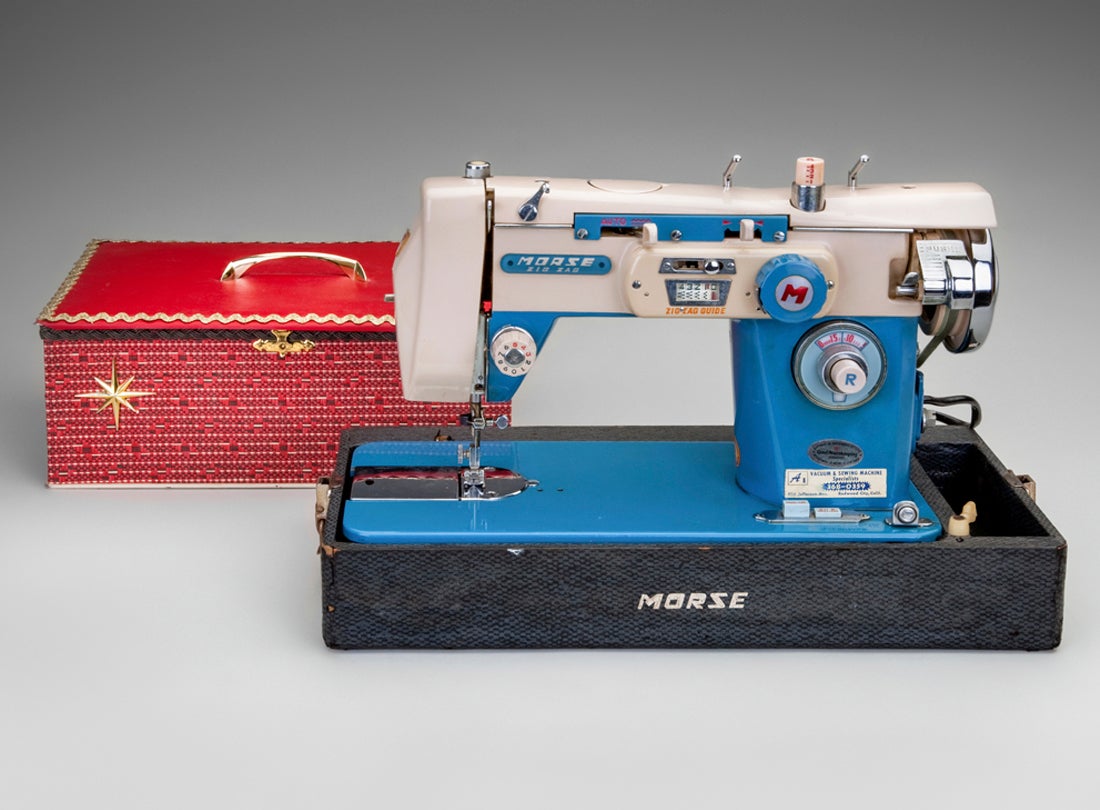
Domestic sewing machine trade card c. 1882
Courtesy of the Library of Congress Prints and Photographs Division, Washington, D.C. LC-DIG-pga-03985
R2011.3414.015
Sewing machine c. 1860
United States
Collection of Lacis Museum of Lace and Textiles, Berkeley, CA
AED 21557
L2011.3402.018
When inventors were first grappling with inventing a sewing machine in the early 1800s, they made many unsuccessful attempts to design a machine that imitated hand sewing. In hand sewing, the needle requires a short length of thread that is forced in and out of the fabric in order to form a stitch. This could not be duplicated by machine, so the challenge lay in creating a new way for a continuous supply of thread to form stitches in fabric. An eye-pointed needle, which does not pass completely through the fabric—rather than a needle with a head and point as used in hand sewing—enabled this to be achieved. Sewing machine inventor Elias Howe (1819–67) attempted to devise a machine that mimicked hand sewing before he eventually fabricated a machine with an eye-pointed needle. But he struggled to convince the public why they should use the laborsaving device. Howe challenged a number of the finest seamstresses in Boston to compete with his machine. Each sewed a seam of the same length. Even though the machine sewed faster than any of the seamstresses, no one placed an order for his novice device. Rather than forcing seamstresses out of business, as many had feared, the sewing machine eventually gained acceptance and increased both employment and garment production.
Sewing machine with treadle c. 1880s
Jones
England
Collection of the Museum of American Heritage, Palo Alto, CA
4M.020
L2011.3401.006
Jennie Pettway and another girl help the quilter Jorena Pettway construct a quilt Gees Bend, Alabama 1937
Photograph by Arthur Rothstein (1915–1985)
Courtesy of the Library of Congress Prints and Photographs Division, Washington, D.C.
LC-DIG-ppmsca-31901
R2011.3414.014
As sewing machines became widely available, home sewers quickly realized the advantages of using the devices in the production of quilts. In the late 1800s, women often combined hand and machine stitching to fabricate quilts. Many machines came with special attachments for sewing quilts. By the 1900s, attachments called jigs allowed quilters to easily sew curved lines in addition to straight stitches. Quilt borders could be finished in a short time with the assistance of a sewing machine. With the reduction of time required for plain stitching utilitarian items such as blankets, many women could devote more time to decorative fancy sewing. For instance, crazy quilts became popular in the 1880s and allowed for a host of decorative hand-embroidered stitchery around the borders of each small piece of fabric that was sewn together.
Sewing machine c. early 1900s
Wilcox and Gibbs
New York
Collection of the Museum of American Heritage, Palo Alto, CA
4M.063
L2011.3401.018
In the early 1850s, the majority of sewing machines were too heavy and cumbersome for home use. In response, James Gibbs designed a relatively inexpensive, lightweight machine. Together with Charles and James Willcox, he founded the Willcox and Gibbs Sewing Machine Company in 1857. Willcox and Gibbs machines made a single thread chain stich with the aid of a rotating hook. Chain-stich machines used only one thread, without the aid of a bobbin. Whereas, the majority of machines used two spools of thread: a bobbin thread from below and a spool of thread from above to produce a lockstitch. The advantage to Willcox and Gibbs machine was that seamstresses did not have to worry about running out of bobbin thread. Part of one cleverly written advertisement declared: “If one thread will do, why bother with two, to break, to confuse, and to tangle?” However, chain stiches unravel if broken at any point, and the direction of the stiches cannot be altered from one stich to the next. Items such as feed sacks, which were later taken apart and re-used as fabric for clothing or towels, were ideal items to be to sewn with this type of machine. These machines were popular because they sold for substantially less than their competitors such as Singer. Willcox and Gibbs made hand and later motorized versions of chain-stich machines until the 1940s. The company eventually produced lockstitch machines and remained in business until 1973.
Sewing box c. 1850
China
Courtesy of Robin Berry
L2011.3404.010
Sewing cases, workboxes, and other special-purpose containers were crafted in various shapes, sizes, and materials, particularly during the late 1700s and throughout the 1800s. Artisans in Italy and France crafted luxurious, velvet-lined boxes made from mahogany and walnut. These boxes often had mirrors on their interior lids and sunken compartments to hold various items. Such boxes were not merely utilitarian containers, but prestigious items meant to be displayed and admired. Many sewing boxes were also made in India and China for the European export market. Craftsmen fabricated boxes from ivory, sandalwood, and tortoiseshell, and decorated them using lacquer or inlay techniques. Sets of finely carved implements, copied from European examples, were included in these boxes.
Sewing box c. 1850
China
Courtesy of Robin Berry
L2011.3404.010
Sewing machine c. 1895–99
Singer
New York
Collection of the Museum of American Heritage, Palo Alto, CA
4M.092
L2011.3401.021
Isaac Singer partnered with Lawyer Edward Clark to form the Singer Company in 1851. The company spent large sums of money on advertising and used more aggressive sales tactics than any of its competitors. Soon after the company established itself, they built lavish sewing machine showrooms staffed by attractive young women who demonstrated their products. This helped ease public doubts about the sewing machine—one of the first modern home appliances that women had to operate. The company also pioneered the practice of selling sewing machines on installment plans, which enabled consumers of varied incomes to purchase them. Early Singer sewing machines sold for approximately $125.00. Most of the parts of each machine were produced by hand, which slowed production. Singer invested in machinery designed to mass-produce sewing machines with interchangeable parts, and in the late 1850s, opened the world’s first mass-production facility for sewing machines. Standardized machines meant that parts could be readily replaced and machines easily repaired. Although the machines sold for about half the price of the earlier models, Singer greatly increased his profit margin, because the mass-produced machines cost approximately $12.00 to produce. By 1860, Singer became the largest sewing machine manufacturer in the world. In 1908, the company built one of the first skyscrapers in New York City.
All nations use Singer sewing machines poster advertisement c. 1892.
R2011.3414.001
Singer trade cards represent the global market that Singer conquered. The company became the leader of the export sewing machine trade. As early as 1861, Singer was selling more machines overseas than in the United States. By 1880, the company had firmly established markets in Europe, Japan, Russia, Mexico, India, Ireland, and South America. The Singer Company manufactured a colossal nine million sewing machines by 1890! Trade cards served as nineteenth-century pocket-sized advertisements for the sewing machine company and its products. Sewing machine salesmen distributed these colorful cards with engaging imagery in hopes that people would save them for their decorative value while being gently reminded of the company’s brand name.
Demorest trade card c. 1860s–70s
Collection of the Lace Museum, Sunnyvale, CA
R2011.3403.034.08
Early nineteenth-century patterns had to be scaled up to create full-sized garments. In 1854, New York milliner Ellen Curtis Demorest (1824–98) revolutionized the world of home sewing. She offered full-scale, fold-out patterns of fashionable garments. However, sewers had to adapt the pattern to their size. In 1860, she introduced Madame Demorest’s Mirror of Fashions, which featured the latest styles from the world’s fashion capitals and included a pattern stapled into the magazine. She also sold patterns individually through mail order. But Madame Demorest failed to patent her invention. The popular magazine Harper’s Bazaar and other publications also began including patterns in each issue, providing competition.
Ebenezer Butterick (1826–1903) patented his tissue paper pattern in 1863. Initially he only made patterns for men’s and children’s wear, but by 1866, he expanded to women’s patterns. Butterick was the first to sell patterns in different sizes. He thought of creating graded patterns in response to his wife’s request for a sized pattern when she was making a garment for their son. Like the sewing machine, graded patterns, revolutionized the industry, saving women hours of time in scaling patterns for individual fit. Patterns were printed on tissue paper, cut, folded, and inserted into envelopes. Detailed instruction sheets explaining how to construct the garment later became available with the patterns.
Sewing machine c. 1890
Frister and Rossmann
Germany
Courtesy of the Museum of American Heritage, Palo Alto, CA
4M.062
L2011.3401.017
Toy sewing machine c. 1940s
Casige
Germany
Courtesy of Beryl Self
L2011.3407.003.004
Toy sewing machine c. 1930
Germany
Collection of Lacis Museum of Lace and Textiles, Berkeley, CA
AED 25599
L2011.3402.024
Toy sewing machine c. 1920
Singer
New York
Collection of Lacis Museum of Lace and Textiles, Berkeley, CA
AED 25587
L2011.3402.031
Toy sewing machines helped to introduce young girls to the domestic art of sewing. Commonly misidentified as salesmen’s samples, these detailed vintage machines were made and marketed as toys or junior machines for little girls. Miniature machines were first made of enameled tinplate or cast iron during the late 1800s. Floral and other pictorial transfers often embellished the toys. Companies such as Singer seized the opportunity to market their products to young girls and their mothers by offering miniature machines. They made their first junior machines in the early 1900s. Singer advertised them as “real sewing machines for little girls” and claimed that they sewed with a “perfectly even stich–just like mother’s big machine.” Cleverly, the company also advertised the machines to mothers as a handy travel-size machine if the need for mending arose.
Sewmaster sewing machine early 1900s
Seawol, Inc.
USA
Collection of the Museum of American Heritage, Palo Alto, CA
L2011.3401.041
Sewing accessory stands c. 1930
USA
Collection of Lacis Museum of Lace and Textiles, Berkeley, CA
AEC 25607
L2011.3402.001-.003
Sewers used handspun linen, wool, or silk thread throughout the 1700s. Cotton yarn or floss was used only for embroidery. By the turn of the nineteenth century, cotton thread first began to be adapted for hand sewing in Scotland. Six-ply cotton thread, developed in the late 1840s, provided more strength from six individual strands twisted together, but was still not entirely capable of enduring the stress of the sewing machine. In the 1860s, the Clark Company of New Jersey introduced an innovation that revolutionized the cotton thread industry. It used three sets of two twisted strands that formed a stronger thread for use in hand or machine sewing. Other manufacturers soon began to offer similar thread.
Elna sewing machine 1940s
Tavaro S. A.
Switzerland
Collection of the Museum of American Heritage, Palo Alto, CA
4M.096
L2011.3401.022
Elna sewing machines were designed and manufactured in Geneva, Switzerland. The original Elna was first offered in 1940. It was the first modern compact, portable, electric sewing machine with a free arm. A free arm is a removable or drop down piece on the bed of the machine that allows one to sew pant legs, cuffs, and other circular hems. The machine, which was made of die-cast metal, had a major influence on the development of the modern household sewing machine. The Elna had a built-in motor, a sewing light, and an all-metal carrying case that converted into an auxiliary sewing table. Nicknamed “the grasshopper,” the green-colored machine was unusual for its time when most machines were offered in black. Nearly a decade later, the Elna Supermatic was introduced in 1953. Unlike the original Elna, the Elna Supermatic offered a zigzag stitch. The groundbreaking model also featured many different decorative stitches, which it made using single or twin needles.
A woman demonstrates the steps in assembling a pattern and fabricating a garment at home for the Office of War Information 1943
Courtesy of the Library of Congress Prints and Photographs Division, Washington, D.C.
LC-USW33-021692-ZC
R.2011.3414.005
During World War II, in an effort to be thrifty, women were encouraged to sew their own clothing at home. The U.S. Department of Agriculture’s Bureau of Home Economics issued booklets on sewing, mending, altering, patching, and restyling old clothing, as well as transforming men’s discarded suits into wearable women’s suits. Companies such as Singer offered free classes at their sewing centers. World War II consumed vast amounts of domestic resources including fabric and metal. Fabric restrictions were issued to the ready-to-wear industry in a calculated effort to conserve approximately 100 million yards of material for use in the war effort. The retail sale of new sewing machines reached a standstill from 1942 to 1945. On the other hand, the pattern industry experienced an unprecedented sales increase during the war due to the greater numbers of home sewers. Butterick and other pattern companies created designs that conformed to the War Board’s regulations. A new, slim silhouette developed with narrower skirts. Shorter lengths were adopted for jackets, skirts, and dresses. Details such as buttons, trims, and appliques were kept to a minimum. Patterns had fewer pieces and required less material.
Quarter-size dress forms c. 1950s–60s
Collection of History San Jose, San Jose, Ca
1985-14-5
L2011.3408.017-.018
Domestic science or domestic arts, later referred to as home economics, has its roots in eighteenth-century needlework and sewing classes. When families could afford it, they sent their daughters to young ladies’ academies, where needlework was an important part of the curriculum in the United States. Domestic science or arts courses were first introduced in public schools around the country in the 1880s and 1890s. Specialized schools in sewing were also established at this time. By the late 1930s, nearly 90 percent of schools in cities and towns with substantial populations offered home economics programs in schools at the junior high and high school levels. Teachers of home economics traditionally made home sewing a critical part of the curriculum, emphasizing self-sufficiency and resourcefulness. Junior high students typically became familiar with the sewing machine and simple hand stitching and mending, while more advanced garment construction was taught at the high school and college levels. Quarter-size dress forms allowed students to create miniature versions of their designs, before crafting the full-size versions.
Sewing machine 1950s
Morse
Japan
Courtesy of K. V. Godshall
L2011.3411.001
Sewing box c. 1950s
USA
Anonymous lender
L2011.3412.001
Shortly after World War II, Japan began to manufacture a large number of sewing machines for both domestic and foreign markets. Many of these colorful, streamlined machines reflect the mid-century modern design aesthetic. The 1950s and 1960s have often been regarded as the golden age of modern home sewing. Advances in sewing machine technology made sewing at home easier then ever before. There was a strong focus on fashion sewing, designer patterns, and copying Hollywood styles. In 1955, approximately 52 million women and girls in the United States spent time sewing. The trend continued in the 1960s, when in 1963, home sewers spent a staggering one billion dollars on sewing products from sewing machines and patterns to fabric and notions.